プラズマの熱を受ける受熱機器の開発
-微細なスパイクによって強力な接着を実現-
核融合科学研究所(NIFS)は、プラズマからの熱を受け止める受熱機器の開発を進めています。今回、NIFSと穴織カーボン株式会社(大阪府)は共同で、従来のカーボン製受熱機器の上に高融点金属であるタングステンを接合する技術を開発しました。
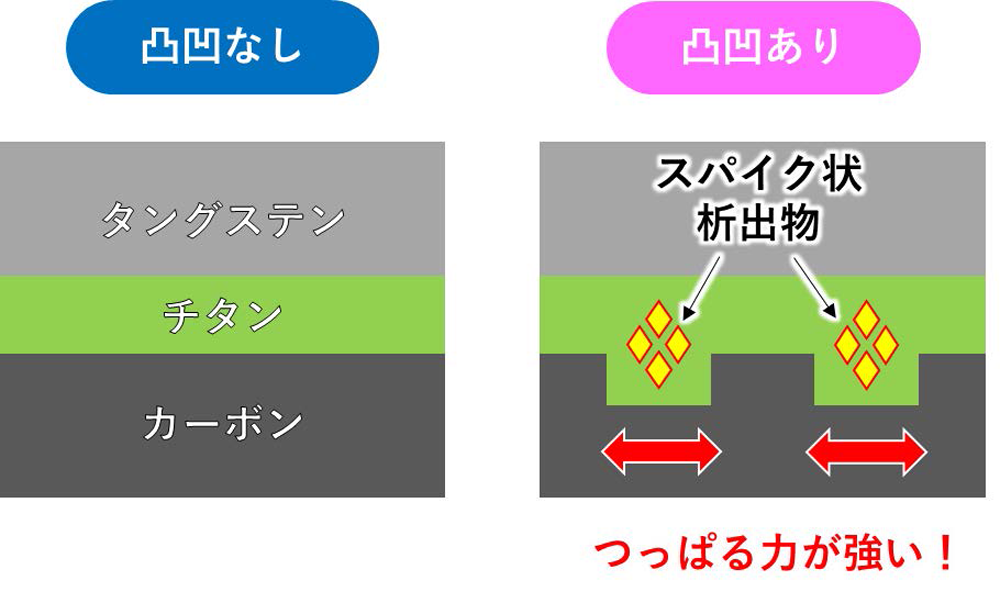
一般に金属などの材料は加熱すると膨張して伸びますが、その伸び方は材料によって異なります。そのため2種類の材料を、熱を加えて貼り合わせる場合、接合面に一方の材料を引っ張る力(熱応力)が発生します。この熱応力が大きくなると、接合面が剥がれたり、材料自体に亀裂が入る恐れがあります。
本研究では、この問題をタングステンとカーボンの間にチタンという金属を挟むことによって解決しました。金属同士の接合において、接合面に他の金属を挿入して熱応力を緩やかにすることはよくあります。特にチタンは色々な金属と仲が良いので、しっかり密着してくれることが期待できます。
ところが、そのようにしてくっつけた接合体がどれくらいの力で割れてしまうのか、専用の試験機で調べたところ、想定していたよりも小さい力で接合面が剥がれることが分かりました。
この問題を解決するために、温度、圧力、時間といった接合条件を様々に変化させてサンプルを作成し、接合力の測定を繰り返しました。しかし、多少の改善はみられたものの、なかなか期待した結果が得られませんでした。
ある時、タングステンやカーボンの表面を、ザラザラに荒らしてみてはどうだろうかと考えました。一般的に金属同士の接合では、接合面がツルツルで平らな方が接合面に空隙ができにくく、強い接合力が得られるとされていますので、この方法は明らかに定説に反しています。
しかし実際には、平らなカーボンの表面に、上の図のよう凸凹構造を部分的に作ることで、強い接合力が得られることが分かりました。この時の接合部の状態を電子顕微鏡などで詳しく観察すると、凸凹の凹の部分にスパイク状の物質が作られていました。このスパイクはチタンとカーボンでできた物質で比較的硬い物質です。我々が開発した接合方法は、大きな電流を流して接合部を加熱するため、凸凹構造による電流経路の変化がスパイク状の物質を析出させるのではないかと考えています。結果的にこのスパイクが、接合面に平行方向の力に対して突っ張ることで、強い抵抗力、すなわち強い接合力を発揮しているものと思われます。
本研究開発で得られた接合技術を用いて、大型ヘリカル装置(LHD)の受熱機器を製作し、第24サイクルのプラズマ実験で使用しました。計8000回以上、高温プラズマに曝されましたが、タングステン表面やタングステンとカーボンの接合界面に目立った損傷は見られませんでした。今後、電子顕微鏡等を用いて、微細な亀裂や損傷がないか詳細に観察する予定です。
本研究は、核融合科学研究所の森崎友宏、村瀬尊則と、穴織カーボン(株)の曽我部敏明、塩崎智広らの共同研究によって進められました。
この研究成果は、プラズマ・核融合学会のオンライン学術論文誌「プラズマ・アンド・フュージョン・リサーチ」に2023年1月30日付で掲載されました。