Development of monitoring and prediction methods of plasma heat load in fusion burning plasmas
In the first wall facing the core plasma and divertor, there is a need to develop a system to detect a concentration or sudden increase in heat load. However, in commercial reactors, the installation of an infrared camera that can observe a large area of the inner wall is not allowed due to the breeding of tritium, which is the fuel of the reactor. We have extended the analytical method to back-calculate the temperature and heat load of the plasma irradiated surface from the data of thermocouples embedded in the metal target and investigated the conditions to reconstruct the spatial distribution of the heat load with the data of a small number of measurement channels.
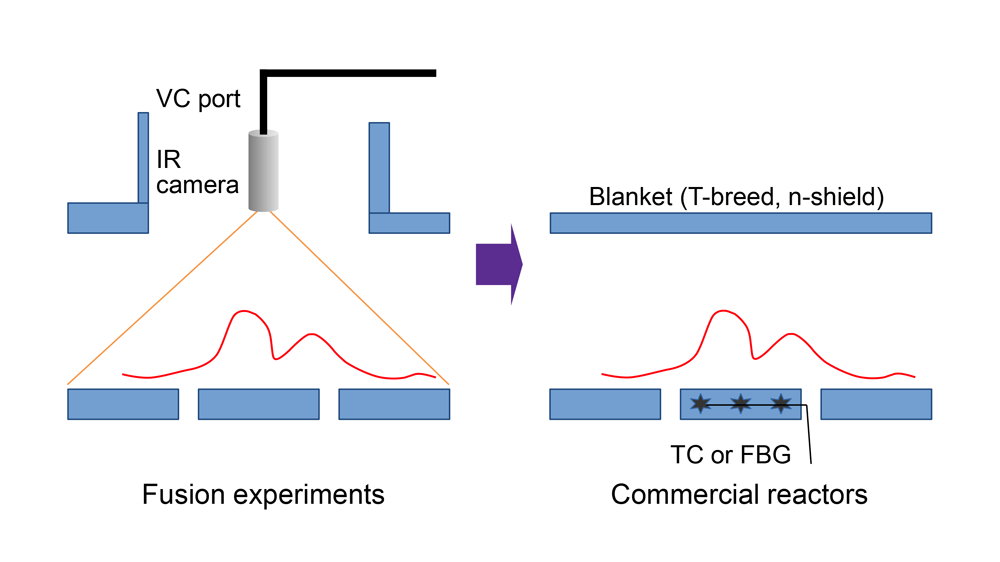
In fusion power generation, the number and size of ports for plasma measurement are extremely limited by the need to breed tritium, one of the fuels, in the blanket surrounding the core plasma. Since it is not possible to monitor the concentration of heat load on the inner walls of the device or the temperature rise on the inner wall surface using infrared cameras and other equipment widely used in current LHDs and other fusion experimental devices, other methods must be used for the maintenance of the fusion reactor. One typical method is to monitor the temperature by attaching thermocouples inside the vessel's inner wall plate, but a method to evaluate the spatial distribution and temporal variation of heat flux from high-temperature plasmas with dynamic fluctuations has been problematic.
The research team has proposed a method to evaluate the time variation of heat flux by mounting a thermocouple inside the plasma facing material, measuring the time variation of temperature at different measurement positions due to heat conduction when the heat flows into the plasma-irradiated surface, and solving the inverse heat conduction equation. While there is a large heat flow from the plasma, the temperature monitored by the thermocouple rises, and when the irradiation is over, the temperature begins to drop. This time variation of the observed temperature lags behind the time variation of the plasma heat flux. The time delay increases as the thermometer moves away from the plasma irradiation surface. The temperature rise during constant heat flux irradiation can be calculated analytically using the heat conduction equation, yielding a one-dimensional temperature response function with respect to the distance from the surface. In previous studies, we have established a method to evaluate the time variation of actual plasma heat flux using this response function.
In this submitted paper, we report the results of a study that extends the temperature response function to two dimensions, to incorporate the effect of the plasma heat flux distribution at the surface of the device's inner wall plate. Using a mathematical method called Fourier decomposition, we extended the temperature response function to two dimensions and proposed a method to reconstruct spatially and temporally varying heat flux distributions from temperature measurement data at different locations.
Using this method, we attempted to reproduce the heat load measurements on the divertor tiles in LHD, where the heat load was concentrated in two lines called divertor traces, and the height and extent of the peaks were observed to vary depending on the plasma conditions, as seen in the infrared camera images. We selected temperature data from a small number of points on the tiles and considered this as data from a virtual thermocouple and attempted to reconstruct the temperature distribution using the two-dimensional temperature response function described above. As a result, we were able to find the conditions for measuring the two-line structures observed in the infrared camera image.
This achievement will make a very important contribution to the design of measurement equipment that is indispensable for the safe operation of actual fusion burning reactors. With the introduction of a highly accurate measurement system, it is possible to quantitatively evaluate the extent of damage to a plasma irradiated surface by analysis using an embedded thermocouples and temperature response function, even when an excessive heat load is applied. Furthermore, this achievement is important for monitoring and precisely controlling the plasma heat load in fusion reactors.
This research was conducted in collaboration with a research group led by Hiroto Matsuura of the Graduate School of Engineering, Osaka Prefecture University, Bui Xuan Nhat Son, then a doctoral student, and Suguru Masuzaki of the National Institute for Fusion Science.
The results of this research were published on March 21, 2024 in Review of Scientific Instruments, a journal of the American Institute of Physics.