New type of divertor heat removal component demonstrated high reliability in large-sized plasma confinement device (LHD)
A new type of divertor heat-removal component with tungsten (W) armor and an oxide-dispersion-strengthened copper (GlidCop®) heat sink (W/GlidCop®) has been developed by new fabrication technology, Advanced Multi-Step Brazing, (AMSB). Then the new component was installed in the divertor strike position of the Large Helical Device (LHD) and exposed to neutral beam injection–heated plasma discharges with 1180 shots (~8000 s) in total. Though submillimeter-scale damage, such as unipolar arc trails and microscale cracks, was identified on the W surface, the extremely high heat removal capability did not show any sign of degradation over the experimental period.
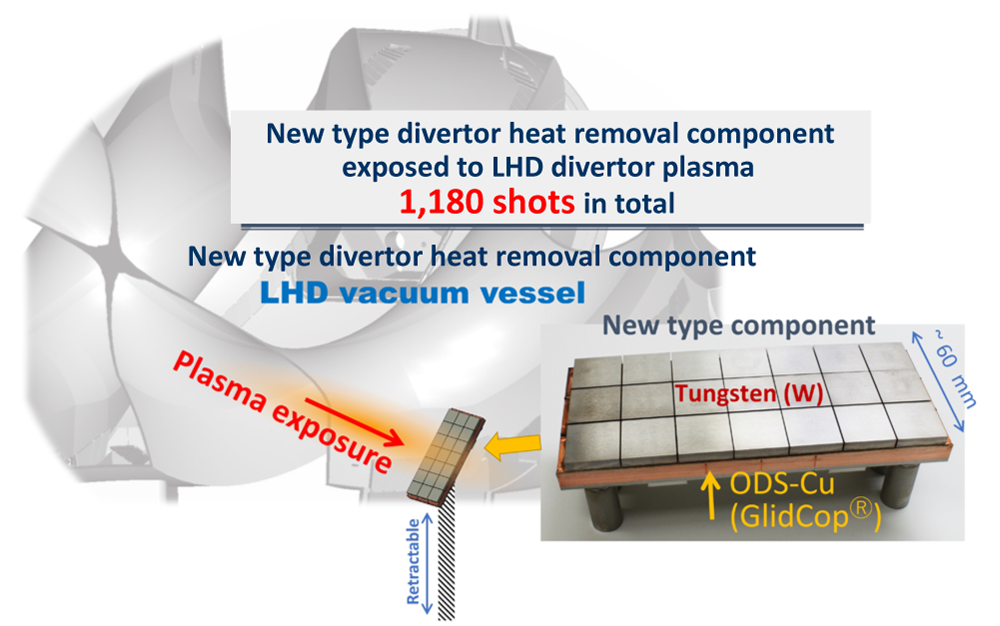
The high heat flux component in a fusion reactor is called a “divertor” in which a candidate structure of the divertor heat removal component is that tungsten (W) armor is jointed on to a copper alloy heat sink. We developed the new type of divertor heat removal component with W armor and an oxide-dispersion-strengthened copper (GlidCop®) by original fabrication technology, so called Advanced Multi-Step Brazing (AMSB), in which the component has a rectangular-shaped cooling flow path channel with a V-shaped staggered-rib structure in the GlidCop® heat sink. This W/GlidCop® component showed an extremely high heat removal capability during a ~30 MW/m2 steady-state heat loading condition in our previous work.
In this work, to investigate durability and Plasma Wall Interactions (PWI) phenomena of the new component against simultaneous loading of high-heat and high-particle flux under a large-sized plasma confinement device, the component was installed in the divertor strike position of the Large Helical Device (LHD), as shown in the graphic, and exposed to neutral beam injection–heated plasma discharges with 1180 shots (~8000 s) in total. After the exposure, several microstructural analyses were conducted by using a dual-beam type of focused-ion beam/scanning electron microscopy (FIB-SEM) device, nanoDUE’T® NB5000 (Hitachi High-Technologies Corp.) on the W armor plate.
An extremely high heat removal response in the component was demonstrated through the quick increase and decrease of the temperature of the W plate located on the divertor strike point during discharges. Though submillimeter-scale damage, such as unipolar arc trails and microscale cracks, were identified on the W surface, such a high heat removal response did not show any sign of degradation during the 1180 shots (~8000 s) of plasma discharges. If this submillimeter-scale damage evolves far beyond the millimeter scale, the heat removal performance will be degraded. The improved component, which has tolerance against repetitive heat loading, will be required for a reactor environment.
From a viewpoint of microstructural damage on the surface of the W armor, remarkable sputtering erosion and redeposition phenomena, due to the strong influx of the divertor plasma, were confirmed on the side surface wall of the W armor. This phenomenon could be caused by the synergistic effects of high-flux and long-time particle loading. Such a high fluence would also be easily reached in future fusion devices. This work has demonstrated one of the critical erosion phenomena of W armor for future fusion devices.
This research result was published in Fusion Science and Technology, a journal on fusion research by the American Nuclear Society on April 10, 2023.